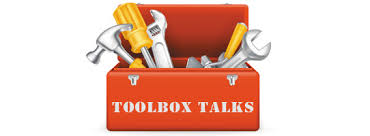
Category: Excavation
Excavation
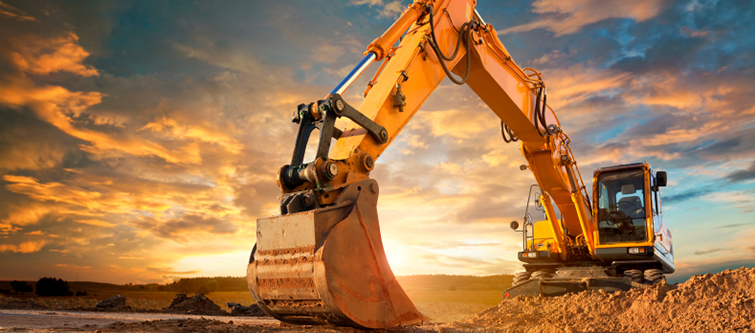
Excavation work is hazardous. This guideline provides information on the potential hazards involved in excavation work so that workers and employers can work together to create a safe, injury and fatality free work site.
DEFINITIONS:
Excavation: means a dug out area of ground and includes a deep foundation excavation, trench, tunnel and shaft.
Open excavation means an excavation in which the width is greater than the depth, measured at the bottom.
Trench means an excavation that is deeper than its width measured at the bottom.
Trench Cage means a steel support structure designed to resist the pressure from the walls of a trench and capable of being moved as a unit.
Trench Jack means a screw or hydraulic jack used as a brace for a temporary support structure.
Shoring is an assembly of structural members designed to prevent earth or material from falling, sliding or rolling into an excavation.
Pile or Caisson means a slender, deep foundation unit made of materials or a combination of materials, such as wood, steel or concrete, which is either pre-manufactured and placed by driving, jacking, jetting or screwing, or cast in place in a hole formed by driving, excavation or boring.
Shaft means a vertical or inclined opening that leads to an underground working and is excavated below ground level.
Support structure means a temporary/permanent structure or device designed to provide protection to workers in an excavation, tunnel or shaft from cave-ins, collapse, sliding or rolling materials and includes shoring, bracing, piles, planks and trench cages.
Tunnel means a generally horizontal excavation that is more than a metre long and located underground.
HAZARDS TO WORKERS NEAR EXCAVATION SITES:
The most common hazards that exist in excavation work include:
- cave-ins or excavation collapses
- excavated material
- falling objects or objects near an excavation
- powered mobile equipment
- slips, trips, and falls
- hazardous atmospheres
- flooding/water hazards
- underground facilities
Cave-Ins or Excavation Collapses:
It is because both employers and workers often forget that when they remove earth from the ground it creates an opening, and the remaining earth surrounding the opening tends to relax. This increases the pressure towards the walls of the opening and makes the ground collapse. Water in the soil or ground also affects the stability of the walls by putting additional pressure on the walls & increasing the possibility of a cave in. Unless a horizontal distance equal to the vertical depth of the excavation walls is maintained, engineering controls must be used (ex: shoring, trench cages) to provide a safe and healthy workplace within the excavation area.
Excavated Material:
Injuries may also occur in excavation work when excavated material on the surface of the excavation is too close to the edge and falls into the excavation, or affects the structural stability of the walls of the excavation. Pile all excavated material so that the material cannot roll back into the excavation. The material must never be closer than one metre (three feet) from the edge of the excavation, and should be placed as far away as possible so it does not affect the structural stability of the walls. Ideally, the excavated material should be placed as far away from the edge of the vertical excavation as the excavation’s height (d ³ h: see diagram below).
Falling Objects or Objects near an Excavation:
Place tools and equipment used at the excavation site so that they cannot fall into the excavation or affect the structural stability of the walls of the excavation. Use barriers to help keep tools and equipment at a safe distance from the edge of the excavation. Use ropes or other lowering devices to transport the tools or equipment into the excavation.
Powered Mobile Equipment
Workers may be exposed to hazards when powered mobile equipment is used near an excavation site. Powered mobile equipment includes backhoes, track hoes, concrete trucks, trucks removing excavated material and others. Common hazards related to powered mobile equipment include:
- equipment placed close to the edge of an excavation may cause the excavation walls to become unstable. Powered mobile equipment can be placed near the edge of the excavation if a support structure, designed to consider the overload from the equipment, is installed in the excavation.
- equipment vibration puts additional pressure on excavation walls, affecting the structural stability.
- equipment operating on rough terrain, or too close to the edge of an excavation, may roll over and fall into the excavation. Ensure all equipment is equipped with roll over protective structures (ROPS).
- workers riding on equipment without approved seats may be injured.
- workers getting on and off equipment are at risk because balance can be affected by the vibration of the equipment. A worker may not be as sure footed getting off the equipment after operating it for a period of time.
- workers may be injured by equipment. A safe distance must be maintained from moving equipment at all times. Operators must be aware of all workers near their work area.
Slips, Trips, and Falls
Slip, trip and fall hazards are common around excavations. Examples include:
excavation entrances and exits. A safe means of entering and exiting an excavation is required. Specifically, where an excavation is more than 1.5 metres (five feet) deep, a stairway, ramp or ladder is required. Workers must use both hands when climbing up or down ladders. Tools or equipment should not be carried up or down the ladder. In addition, the ladder must:
- meet the standards outlined in the Workplace Safety and Health Regulation, respecting Entrances, Exits, Stairways and Ladders.
- extend one metre above the edge of the excavation
- be located no more than three metres (10 feet) away from the workers inside the excavation.
uneven ground surfaces around or inside an excavation. It is important that a housekeeping program is in place and every effort is made to ensure walkways and pedestrian traffic areas are maintained.
Hazardous Atmospheres:![]()
Hazardous atmospheres at excavation site may come from soils that are moved or from pipes and conduits disturbed during excavation. Where there is a potential for a hazardous atmosphere, a plan must be developed to ensure the workers in or near the excavation are not at risk. The plan must include the following steps:
Pre-Work Testing – The atmosphere must be tested before anyone enters the excavation to ensure they won’t be exposed to hazards. Common atmospheric hazards include gasoline vapours, methane or other explosive gases and a lack of oxygen.
Periodic Testing – Periodic tests must be conducted to ensure the hazardous atmosphere is controlled and that workers are protected. All testing must be done by qualified personnel who have the knowledge and expertise required to keep workers safe. All tests conducted must be:
- recorded
- kept at the excavation site
- made available to the workers upon request
Flooding/Water Hazards:
Because of the condition or location of excavation sites, water hazards may be present, including:
Flooding – An excavation may flood if the work is below the water table, near a watercourse bank or exposed to adverse weather conditions. When there is a risk of flooding, an emergency evacuation plan must be developed. The plan will include a full body harness with a lifeline (that meets the requirements of Part 14 of the Workplace Safety and Health Regulation, relating to fall protection) to be worn by workers in the excavation. Workers must also have direct communication with the person located at the surface of the excavation.
Water Accumulation – This may be caused by an excavation near a ground water source, in wet conditions or because of equipment that uses water for operation near the excavation site. Water accumulation must be kept to a minimum to reduce risks such as slipping or tripping hazards, electrical hazards, equipment malfunctions or others.
Underground Facilities
Common underground facilities include:
- electrical lines
- oil and gas lines
- telecommunication lines (phone, cable, computer)
- water and sewer lines
- traffic signal lines
- steam lines
Special attention must be given to the hazards associated with underground facilities. Before beginning excavation work, proper planning must identify the location of underground facilities and any precautions needed to avoid contact with these facilities.
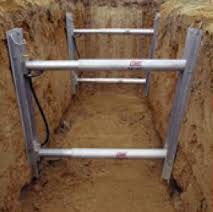
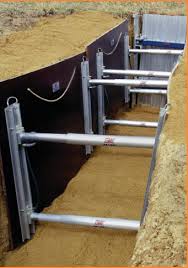
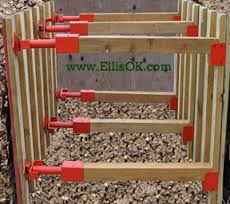
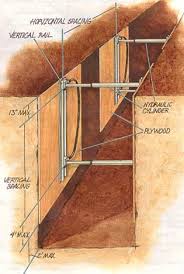