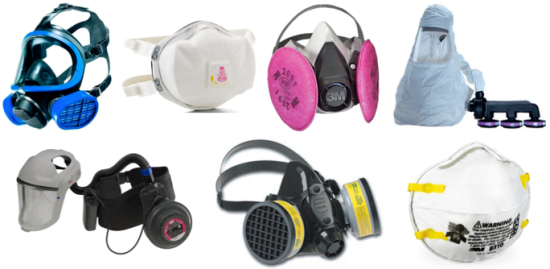
What is mean by respirator fit test?
A fit test is a test protocol conducted to verify that a respirator is both comfortable and correctly fits the user. Fit testing uses a test agent, either qualitatively detected by the wearer’s sense of taste, smell or involuntary cough (irritant smoke) or quantitatively measured by an instrument, to verify the respirator’s fit. See questions related to qualitative and quantitative fit testing for more specific information.
Fit testing necessary:
Fit testing each model of respirator the employee is to use in workplace tasks before their use is important to assure the expected level of protection is provided by minimizing the total amount of contaminant leakage into the face piece. The benefits of this testing include better protection for the employee and verification that the employee is wearing a correctly-fitting model and size of respirator. Higher than expected exposures to a contaminate may occur if users have poor face seals with the respirator, which can result in excessive leakage.
Different methods for respirator fit testing:
Fit test methods are classified as either qualitative or quantitative, and there are multiple protocols of each classification that are OSHA-accepted, ANSI-accepted, or NIOSH-recommended. A qualitative fit test is a pass/fail test to assess the adequacy of respirator fit that relies on the individual’s sensory detection of a test agent. A quantitative fit test numerically measures the effectiveness of the respirator to seal with the wearer’s face, without relying on the wearer’s voluntary or involuntary response to a test agent.
Qualitative fit testing (QLFT):
- The protocols are initiated by first determining the wearer’s ability to detect the test agent (e.g. saccharin, isoamyl acetate, BitrexTM) at a sensitivity level that corresponds to less than an acceptable fit before put on (donning) the tight-fitting face piece respirator. The wearer enters an exposure chamber, has a test enclosure placed on his/her head, or is positioned somewhere in an open test area and the test agent is generated around him/her. The wearer signals when the test agent is sensed. The fit test operator proceeds with the fit test only if the demonstrated sensitization level is low enough to assure the test agent will be sensed at all levels representing a failure to achieve an acceptable fit. [Note: Isoamyl acetate, being an organic vapor, can not be used as a test agent for particulate respirators.]
- Next, the wearer follows the manufacturer’s instructions to put on what initially seems to be the best fitting respirator provided by the employer.
- The wearer then completes a user seal check to confirm that the respirator is properly seated on the face
- The wearer then enters an exposure chamber, has a test enclosure placed on his/her head, or is positioned somewhere in an open test area. The test agent is generated at the designated test level around the subject.
- The fit test operator observes the worker during exposure while directing him/her through a series of exercises. The fit test operator notes involuntary coughing (irritant smoke) during the test or asks the wearer at the end of the test if he or she smelled or tasted anything at any time during the test. From the test subject’s response and the fit test operator’s observations, the fit test operator determines a pass/fail judgment by which the respirator make, model and size may be assigned to the wearer.
How is qualitative fit testing performed?
The Occupational Safety and Health Administration (OSHA) has included the acceptance of respirator fit test protocols in it’s regulations at 29 CFR 1910.134. The OSHA-accepted fit test protocols can be found at 29 CFR 1910.134 appendix A. The American National Standards Institute’s ANSI Z88.10, Respirator Fit Testing Methods provides the step-by-step explanations for conducting the ANSI-accepted fit tests. While the OSHA regulations and ANSI Z88.10 provide the procedures that must be used to conduct each of the accepted protocols, a general description of how theprotocols are conducted is provided below for the convenience of the reader.
Quantitative fit testing performed:
The Occupational Safety and Health Administration (OSHA)has included the acceptance ofrespirator fit test protocols in it’s regulations at 29 CFR 1910.134. The OSHA-accepted fit test protocols can be found at 29 CFR 1910.134 appendix A. The American National Standards Institute’s ANSI Z88.10, Respirator Fit Testing Methods provides the step-by-step explanations for conducting the ANSI -accepted fit tests. There are several methods with significantly different protocols for conducting Quantitative fit testing (QNFT). While the OSHA regulations and ANSI Z88.10 provide the procedures that must be used to conduct each of the accepted protocols, a general description of the most common methods used in the protocols are provided below for the convenience of the reader.
In order to do these measurements, a small sampling tube is positioned to sample the air within the facepiece of the respirator and attached to a fit testing instrument able to calculate the percentage of particles leaking into the facepiece.
- First, the wearer dons one of the respirator models/sizes provided by the employer that is expected to provide a good fit , in accordance with the manufacturer’s instructions
- The wearer completes a user seal check to confirm that the respirator is properly seated on his/her face
- A fit testing adaptor is affixed to the respirator and the respirator is attached to a fit testing instrument through a small sampling tube positioned within the facepiece
- The fit test operator then instructs the wearer to go through a series of prescribed exercises while the attached fit testing instrument measures the ratio of particles both inside and outside of the respirator. From this data, a fit factor for the tested wearer is calculated which will determine whether or not the model, brand, and size of the respirator is suitable (passable) to be used regularly by that wearer.
Difference between a qualitative and quantitative fit test:
Qualitative fit testing (QLFT) relies on the respirator wearer’s senses to determine if there is a gap in the seal of the respirator to the wearer’s face.
The test agents used in the OSHA-accepted and ANSI-accepted qualitative fit testing protocols are:
- Saccharin – a sweet tasting solid aerosol;
- Isoamyl acetate – a liquid that produces a sweet smelling vapor similar to bananas;
- BitrexTM – a bitter tasting solid aerosol; and
- Irritant smoke – a solid aerosol made of stannic oxychloride that produces hydrochloric acid when it comes in contact with water vapor. Exposure to the hydrochloric acid produces an involuntary cough reflex.[Note: NIOSH does not endorse or recommend the use of the irritant smoke fit test. NIOSH, in its formal comments to OSHA on the proposed revision of 29 CFR 1910, 1915, and 1926, strongly recommended against the use of this fit test method because of the health risk associated with exposure to the irritant smoke. That recommendation was primarily based on studies conducted as part of a NIOSH HHE (HETA 93-040-2315) and described in Appendix A of the NIOSH comments to OSHA dated May 15, 1995 (docket H-049).]
The test protocols include testing at a sensitivity level that demonstrates the user will be able to appropriately sense the presence of the test agent within the respirator by taste, smell or the urge to cough.
Quantitative fit testing (QNFT) uses fit testing instrument(s) to provide quantitative, or numerical measurements of the amount of face seal leakage present when a given respirator is donned by a particular user.
Respirator fit tests required:
The Occupational Safety and Health Administration (OSHA) (29 CFR 1910.134) requires a respirator fit test to confirm the fit of any respirator that forms a tight seal on the wear’s face before it is to be used in the workplace. That same OSHA respirator standard also prohibits tight fitting respirators to be worn by workers who have facial hair that comes between the sealing surface of the facepiece and the face of the wearer.
How often must fit testing be done?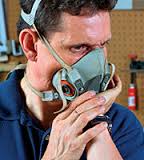
Because each brand, model, and size of particulate facepiece respirators will fit slightly differently, a user should engage in a fit test every time a new model, manufacture type/brand, or size is worn. Also, if weight fluctuates or facial/dental alterations occur, a fit test should be done again to ensure the respirator remains effective. Otherwise, fit testing should be completed at least annually to ensure continued adequate fit.
Once I am fit tested can I use any brand / make / model respirator as long as it is the same size?
No. A fit test only qualifies the user to put on (don) the specific brand/make/model of respirator with which an acceptable fit testing result was achieved. Users should only wear the specific brand, model, and size respirators that he or she wore during successful fit tests. [Note: respirator sizing is variable and not standardized across models or brands. For example a medium in one model may not offer the same fit as a different manufacturer’s medium model.]
Respirator user seal check:
It is a procedure conducted by the respirator wearer to determine if the respirator is properly seated to the face. The user seal check can be either a positive pressure or negative pressure check, which are generally performed as follows: The positive pressure user seal check is where the person wearing the respirator exhales gently while blocking the path for exhaled breath to exit the facepiece. A successful check is when the facepiece is slightly pressurized before increased pressure causes outward leakage. The negative pressure user seal check is where the person wearing the respirator inhales sharply while blocking the paths for inhaled breath to enter the facepiece. A successful check is when the facepiece collapses slightly under the negative pressure that is created with this procedure. A user seal check is sometimes referred to as a fit check. A user seal check should be completed each time the respirator is put on (donned). It is only applicable when a respirator has already been successfully fit tested on the individual.
When should a user seal check be done?
Once a fit test has been done to determine the best model and size of respirator for a particular user, a user seal check should be done by the user every time the respirator is to be worn to ensure an adequate seal is achieved.
User seal check on a particulate respirator:
A user seal check may be accomplished by using the procedures recommended by the manufacturer of the respirator. This information can be found on the box or individual respirator packaging. There are positive and negative pressure seal checks and not every respirator can be checked using both. You should refer to the manufacturer’s instructions for conducting user seal checks on any specific respirator .
The following positive and negative user seal check procedures for filtering facepiece respirators are provided as examples of how to perform these procedures.
Positive pressure check –Once the particulate respirator is properly put on (donned), your hands over the facepiece, covering as much surface area as possible. Exhale gently into the facepiece. The face fit is considered satisfactory if a slight positive pressure is being built up inside the facepiece without any evidence of outward leakage of air at the seal. Examples of such evidence would be the feeling of air trickling onto the your face along the seal of the facepiece, fogging of your glasses, or a lack of pressure being built up inside the facepiece.
If the particulate respirator has an exhalation valve, then performing a positive pressure check may be impossible. If so, then do a negative pressure check.
Negative pressure check – Negative pressure seal checks are conducted on particulate respirators that have exhalation valves. To conduct a negative pressure user seal check, cover the filter surface with your hands as much as possible and then inhale. The facepiece should collapse on your face and you should not feel air passing between your face and the facepiece.
Powered Air-Purifying Respirators (PAPRs) require fit testing
The answer to this question depends on the type of facepiece that the respirator has. Any facepieces that form a tight seal to the wearer’s face, e.g. half-masks and full facepieces must be fit tested regardless of the mode of operation. The PAPR fit test is conducted with the blower turned off.
Loose fitting respirators, such as PAPRs, in which the hood or helmet are designed to form only a partial seal with the wearer’s face or hoods which seal loosely around the wearer’s neck or shoulders, do not require fit testing.
Respirator Fit kit test video
OSHA Respirator fit test video
Click the below link to download about respirator fit test documents and guidelines