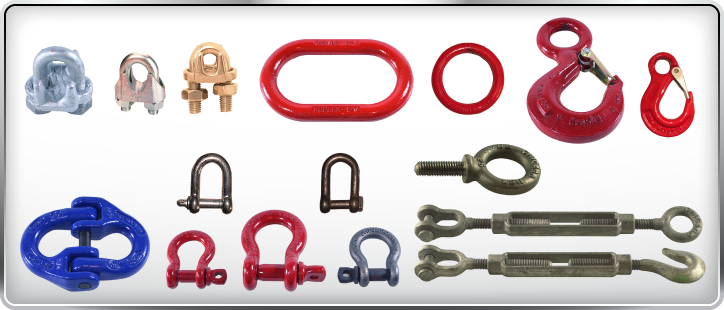
Contents
Rigging Hardware
Introduction:
This Standard applies to the construction, installation, operation, inspection, maintenance, and safe use of lifting equipment used in construction and industrial settings. This includes, but is not limited to: articulating boom, container, gantry, mobile, pedestal, portal, tower and stacker cranes; balance-lifting units; below-the hook lifting devices; cable ways; derricks; jacks; hoists; hooks; loads suspended from rotor craft; material placement systems; monorails; rigging hardware; and scrap and material handlers.
This Standard does not apply to track and automotive jacks, railway or automobile wrecking cranes, shipboard cranes, shipboard cargo-handling equipment, well-drilling derricks, skip hoists, mine hoists, truck body hoists, car or barge pullers, conveyors, excavating equipment, or equipment falling
Purpose:
This Standard is designed to:
(a) guard against and minimize injury to workers, and otherwise provide for the protection of life, limb, and property by prescribing safety requirements
(b) provide direction to owners, employers, supervisors, and others concerned with, or responsible for, its application
(c) guide governments and other regulatory bodies in the development, promulgation, and enforcement of appropriate safety directives
This hardware includes:
- shackles,
- links,
- rings,
- swivels,
- turnbuckles,
- eye bolts,
- hoist rings,
- wire rope clips,
- wedge sockets, and
- rigging blocks.
Definitions:
Abnormal operating conditions: environmental conditions that are unfavorable, harmful, or detrimental to or for the operation of a piece of detachable hardware, such as excessively high or low ambient temperatures; exposure to weather; corrosive fumes; dust laden or moisture laden atmospheres; and hazardous locations. angle of loading: the acute angle between horizontal and the leg of the rigging, often referred to as the horizontal angle.
bow, shackle: the curved portion of the shackle body opposite the pin, often referred to as the bail, the body, the die, or the bowl
dead end: the section of wire rope that is not tensioned under load
design factor: ratio between nominal or minimum breaking strength and rated load of the rigging hardware.
designated person: a person who is selected or assigned by the employer or employer’s representative as being competent to perform specific duties.
ears,shackle: portion of the shackle body which supports the shackle pin
hardware service:
- normal: service that involves use of loads at or below the rated load.
- severe: service that involves normal service coupled with abnormal rigging or operating conditions.
shackle: a U-shaped load-bearing connector designed to be used with a removable pin .
shock load: any condition which causes a momentary increase in the forces in a load-supporting component beyond the weight of the actual load being lifted.
pin, shackle: a steel bolt made to span the two shackle ears .
primary load fitting: the fitting on a rigging block that carries the highest applied load during use.
proof load: the specific load applied in performance of the proof tests.
proof test: a nondestructive load test made to a specific multiple of the rated load of the rigging hardware.
qualified person: a person who, by possession of a recognized degree in an applicable field or certificate of professional standing, or who, by extensive knowledge, training, and experience, has successfully demonstrated the ability to solve or resolve problems relating to the subject matter and work.
rated load: the maximum allowable working load established by the rigging hardware manufacturer. The terms “rated capacity” and “working load limit” are commonly used to describe rated load.
turnbuckle: an adjustable device consisting of three primary components: a body, a right-hand threaded endfitting, and a left-hand threaded end fitting
Shackles – Selection, Use, and Maintenance:
Types and materials:
(a) Body types covered are anchor, chain, and synthetic sling (see Fig. 1).
(b) Pin types covered are screw pin and bolt-type (see Fig. 1).
(c) Shackles other than those detailed in this chapter shall be used only in accordance with recommendations of the shackle manufacturer or a qualified person.
The shackle shall have sufficient ductility to permanently deform before losing the ability to support the load at the temperatures at which the manufacturer has specified for use.
Design factor:
(a) The design factor for shackles up to and including a 150 ton rated load shall be a minimum of 5.
(b) The design factor for shackles over 150 ton rated load shall be a minimum of 4.
Rated loads:
Rated load shall be in accordance with the recommendation of the shackle manufacturer. The terms “rated capacity” and “working load limit” are commonly used to describe rated load.
Proof Test Requirements:
(a) Shackles are not required to be proof tested unless specified by the purchaser.
(b) If proof tested, a shackle shall be inspected after the test for the conditions stated.
Proof Load Requirements:
(a) The proof load for a shackle up to and including a 150 ton rated load shall be a minimum of 2 and a maximum of 2.2 times the rated load unless approved by the manufacturer.
(b) The proof load for a shackle over a 150 ton rated load shall be a minimum of 1.33 and a maximum of 2 times the rated load unless approved by the manufacturer.
Identification:
Shackle Body Identification:
Each new shackle body shall have forged, cast, or die stamped markings by the manufacturer to show
(a) name or trademark of manufacturer
(b) rated load
(c) size
Shackle Pin Identification:
Each new shackle pin shall have forged, cast, or diestamped markings by the manufacturer to show
(a) name or trademark of manufacturer
(b) grade, material type, or load rating
Maintenance of Identification:
Shackle identification should be maintained by the user so as to be legible throughout the life of the shackle.
Effect of Environment:
Temperature:
When shackles are to be used at temperatures above400°F (204°C) or below 40°F (40°C), the shackle manufacturer or a qualified person should be consulted.
Chemically Active Environments:
The strength of shackles can be affected by chemicallyactive environments such as caustic or acid substances or fumes. The shackle manufacturer or a qualified person should be consulted before shackles are used in chemically active environments.
Inspection, Repair and Removal: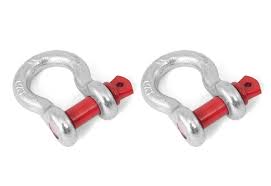
Initial Inspection:
Prior to use, all new, altered, modified, or repaired shackles shall be inspected by a designated person to verify compliance with the applicable provisions of this Chapter. Written records are not required.
Frequent Inspection:
(a) A visual inspection shall be performed by the user or other designated person each day before the shackle is used. Semi-permanent and inaccessible locations where frequent inspections are not feasible shall have periodic inspections performed.
(b) Conditions such as those listed or any other condition that may result in a hazard shall cause the shackle to be removed from service. Shackles shall not be returned to service until approved by a qualified person.
Periodic Inspection:
(a) A complete inspection of the shackle shall be performed by a designated person. The shackle shall be examined for conditions such as those listed and a determination made as to whether they constitute a hazard.
(b) Periodic Inspection Frequency. Periodic inspection intervals shall not exceed one year. The frequency of periodic inspections should be based on
(1) frequency of shackle use
(2) severity of service conditions
(3) nature of lifts being made
(4) experience gained on the service life of shackles used in similar circumstances
(5) Guidelines for the time intervals are
- (a) normal service – yearly
- (b) severe service – monthly to quarterly
- (c) special service – as recommended by a qualified person
Removal Criteria:
Shackles shall be removed from service if damage such as the following is visible and shall only be returned to service when approved by a qualified person:
(a) missing or illegible manufacturer’s name or trademark and/or rated load identification
(b) indications of heat damage including weld spatter or arc strikes
(c) excessive pitting or corrosion
(d) bent, twisted, distorted, stretched, elongated, cracked, or broken load-bearing components
(e) excessive nicks or gouges
( f) a 10% reduction of the original or catalog dimension at any point around the body or pin
(g) incomplete pin engagement
(h) excessive thread damage
(i) evidence of unauthorized welding
(j) other conditions, including visible damage, that cause doubt as to the continued use of the shackle.
Repairs and Modifications:
(a) Repairs, alterations, or modifications shall be as specified by the shackle manufacturer or a qualified person.
(b) Replacement parts, such as pins, shall meet or exceed the original equipment manufacturer’s specifications.
Operating Practices:
Shackle Selection
(a) Shackles having suitable characteristics for the type of sling, load, hitch, and environment shall be selected in accordance with the shackle manufacturer’s data.
NOTE: The angle of loading affects the stress in the shackle. As the horizontal angle decreases, the stress increases in the shackle (see Fig. 2).
(b) The rated load of the shackle shall not be exceeded.
(c) Shackles that appear to be damaged shall not be used until inspected and accepted as usable under Section
Cautions to Personnel:
(a) All portions of the human body shall be kept from between the shackle, the load, and any other rigging during the lift.
(b) Personnel should stand clear of the suspended load.
(c) Personnel shall not ride the shackle.
Storage & Work Environments:
(a) Shackles should be stored in an area where they will not be subjected to damage, corrosive action, or extreme heat.
Rigging Practices:
(a) The screw pin shall be fully engaged, with the shoulder in contact with the shackle body (see Fig. 3).
(b) If a shackle is designed for a cotter pin,it shall be used and maintained in good working condition.
(c) Contact with sharp edges that could damage the shackle should be avoided.
(d) Shock loading should be avoided.
(e) The load applied to the shackle should be centered in the bow of the shackle to prevent side loading of the shackle.
( f ) Multiple sling legs should not be applied to the shackle pin.
(g) If the shackle is to be side loaded, the rated load shall be reduced according to the recommendations of the manufacturer or a qualified person (see Fig. 4).
(h) The screw pin shackle shall not be rigged in a manner that would cause the pin to unscrew.
(i) For long-term installations, bolt type shackles should be used; if screw pin type shackles are used, the pin shall be secured from rotation or loosening.
(j) Shackles should not be dragged on an abrasive surface.
(k) Multiple slings in the body of a shackle shall not exceed 120 deg included angle.
(l) When a shackle is used in a choker hitch, the pin shall be connected to the choking eye of the sling.
Shackles are used for connecting various pieces of rigging equipment together: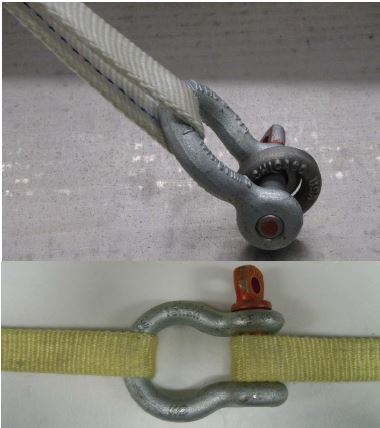
Used as a connecting link between items
- Strap to hoist ring or eye bolt
- Strap to strap
- Used as single attach point for multiple straps
Load rating based on:
- Size
- Material
- Many different types and sizes
Examples of shackle usage:
Side loading of screw pin and bolt type shackles results in a reduction of the working load limit
Shackle rigging practices for Crosby shackles:
Shackle rigging practices with synthetic slings:
- Folding, bunching, or pinching of synthetic slings can occur when used with shackles
- Folding, bunching, and pinching of synthetic slings reduces the sling load rating and must be avoided
Shackle rigging practices:
- Screw pins shall be fully engaged.
- If designed for a cotter pin, it shall be used and maintained.
- Applied load should be centered in the bow to prevent side loading.
- Multiple sling legs must not be applied to the pin.
- If the shackle is side loaded, the rated load shall be reduced.
- Never have the pin against the live line in a choker. The pin must go through the bow of the sling.
Shackle Do’s:
- Visually inspect shackles for any damage or wear on ring and pin.
- Insure shackles have proper identification markings.
- Finger tighten the pin into ring of shackle.
- Check for proper fit of the pin into ring.
- Check the load ratings and use according to manufacturer recommendations.
Shackle Don’s:
- Do not use a shackle if it is bent, damaged, or has been modified.
- Do not use if the shackle does not have proper identification markings.
- Do not use a tool to tighten a shackle pin.
- Do not repair, replace, or modify a shackle.
- Do not use a shackle if the pin has been replaced with a bolt.
- Do not use a hook larger than the diameter of the shackle opening.
- Never exceed the load rating.
Click the below link to download the rigging hardware safety check sheet